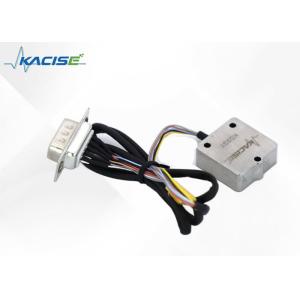
Add to Cart
The KQ3GY gyroscope is a cutting-edge device that was developed using quartz MEMS technology. This advanced technology enables the gyroscope to sense the angular velocities of multiple axes, which can be configured according to the customer's specific needs. Additionally, the KQ3GY gyroscope is capable of outputting digital information through the serial port, making it an ideal option for a wide range of applications.
MEMS technology refers to micro-devices or systems that integrate several components such as micro-sensors, micro-actuators, micro-mechanical structures, micro-power and micro-energy, signal processing and control circuits, high-performance electronic integrated devices, interfaces and communication. MEMS is an independent intelligent system that can be mass-produced, and they typically have a system size of a few millimeters or even smaller. Moreover, the internal structure of MEMS devices is generally in the order of microns or even nanometers, which highlights the exceptional precision of the technology.
MEMS sensors are available in various types, including accelerometers, optical sensors, pressure sensors, gyroscopes, humidity sensors, and gas sensors. These sensors function on their own or integrated with other MEMS devices. MEMS technology plays a significant role in several industries, including healthcare, automotive, aerospace, and consumer electronics, among others.
● Large-scale production
● Short startup time
● Wide operating temperature range
● Low power consumption
● High reliability
● Small size and light weight
● Serial output
Parameter | KQ3Gy |
Power Requirements | |
Input Voltage | 5±0.2 Vdc |
Input Current | < 50 mA |
Performance | |
Measurement range | ±100 |
Bias | ≤0.03 |
Bias stability | ≤20 |
Bias repeatability | ≤20 |
Scale factor nonlinearity | ≤200 |
random walk | ≤0.25 |
Threshold | ≤0.005 |
Bandwidth | ≥140 |
Acceleration correlation | ≤0.01 |
Cross coupling | ≤1 |
Environments | |
Working temperature | -40℃~+65℃ |
Random vibration | 6.06g rms |
Dimensions:
Unit:mm
Airborne instrument measurement refers to the use of instruments in aircraft to collect data on various parameters. These instruments measure atmospheric conditions, aircraft performance, and other critical data required for aviation safety. Examples of such instruments include altimeters, airspeed indicators, and flight data recorders.
A robot is a machine that is designed to perform specific tasks, either programmable or remotely controlled. In aviation, robots can be used for various operations, including monitoring and maintenance of aircraft, ground support equipment, and inspection of critical aircraft components. They can also be used to improve efficiency in manufacturing and assembly processes.
Automated testing refers to the use of software tools to perform tests and verify outcomes without human intervention. In aviation, automated testing is beneficial in the testing and validation of avionics systems, flight control systems, and other critical aircraft components. It helps to improve safety by identifying faults and potential problems before they occur and contribute to accidents.
An attitude reference system is a set of instruments that is used to determine an aircraft's position relative to the horizon. These instruments measure pitch, roll, and yaw angles and provide critical information to pilots for maneuvering the aircraft. They are crucial in maintaining aircraft stability and safety.
A control system is a system that is used to manage and regulate a process by using feedback. In aviation, control systems are used to manage various aircraft functions, including engine and flight control. These systems help to ensure that the aircraft operates safely and efficiently.
Flight test is a process that involves testing an aircraft's performance and handling characteristics in actual flight conditions. It is used to evaluate aircraft design, performance, and safety to ensure compliance with aviation regulations. Flight testing provides critical data that is used to improve aircraft design and safety.
Platform stability refers to the ability of an aircraft or other platform to maintain a stable position without significant deviation. Stability is critical in aviation, as it helps to ensure passenger comfort, safety, and efficient operation of the aircraft. Various factors affect platform stability, including aircraft design, pilot input, and environmental conditions.
Our Electronic Gyroscope Sensor is designed with precision to provide reliable performance for your applications. Our support includes detailed product documentation, an extensive online knowledge base, and troubleshooting guides to help you resolve any issues you may encounter.
We are committed to the satisfaction of our customers and strive to provide exceptional after-sales support. Should you have any feedback or suggestions, we welcome your input as it helps us to continuously improve our products and services.
Product Packaging:
The Electronic Gyroscope Sensor product will be packaged in a sturdy cardboard box with foam inserts to ensure safe transport. The product will be sealed in a plastic bag to protect it from moisture and dust. The box will be labeled with the product name, brand, and barcode for easy identification.
Shipping:
The product will be shipped via standard ground shipping. We will ensure that the product is shipped within 2 business days after receiving the order. The shipping cost will be calculated based on the weight and destination of the package. Customers will receive a tracking number via email once the product has been shipped.